5 min. read
Fluid dispensing has come a long way. In the early days, the only dispensing option was to use a plunger to manually push fluid out of a syringe. With the rapid advancement in technology, today there are various dispensing techniques available, with quite a few dispensing equipment options. They range from simple manual dispensing devices to sophisticated piezo-actuated jetting valves.
Faced with too many choices, selecting the right valve can be a daunting task if you are not familiar with dispensing technology. Here is an overview, from the simplest to the most advanced technologies out there, to help you select the right dispensing system for your applications.
TOPICS COVERED
- Manual Syringe System
- Time/Pressure Dispensing
- Pinch Tube Valve
- Diaphragm Valve
- Needle Valve
- Spool Valve
- Rotary Auger Valve
- Spray Valve
- Progressive Cavity (PC) Pump
- Jet Valve
MANUAL SYRINGE SYSTEM
The simplest way to dispense fluid is through a manual dispensing process. A typical manual system includes a plunger with a piston and a syringe filled with fluid. The operator simply pushes the plunger down until enough fluid is dispensed on the workpiece, either by hand or with the use of a manual syringe gun.
Repeatability rates depend entirely on how consistently the operator can repeat the process. This method is suitable for low-volume applications where product yields below 80% are acceptable.
TIME/PRESSURE DISPENSING
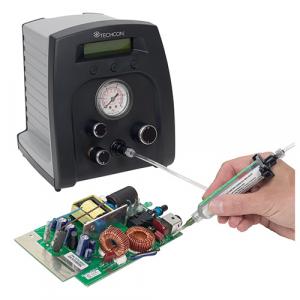
The next step up in process improvement is the Time/Pressure dispensing (TPD) technique. As the name indicates, this technique utilizes air pressure coupled with a control timing circuit to help increase product throughput and yields. Because of the simplicity and decent repeatability rate, over 60% of dispensing applications are done by this technique. Techcon offers a complete range of TPD equipment and accessories that include syringes, needles, receiver heads, pressure containers, valves, and controllers.
The basic TPD syringe system starts with a dispenser, air power syringe, and receiver head assembly. The syringe, filled with fluid to be dispensed, is connected to the time/pressure dispenser via the receiver head assembly. Appropriate air pressure and dispense time are then set accordingly on the dispenser.
After the setup is done, the operator can activate the dispense cycle by simply pressing a foot switch or finger switch. During operation, the dispenser delivers a measured amount of air pressure for a preset dispense time to the syringe. The controlled shot of air forces the fluid out of the syringe, through the dispensing needle, and onto the work surface.
The image above shows the TS250 Series dispenser from Techcon. A precision dispenser that features a digital timer to dispense small dots of fluid accurately from a syringe is widely used in most benchtop applications because it has proven to be the most accurate and repeatable on the market. Typical applications include dispensing solder paste on PCBs for rework and dispensing all types of bonding adhesives.
The disadvantage of the syringe system is it depends on too many variables to maintain a good repeatability rate for the entire dispensing process. One of the variables is the internal diameter of the syringe. If the internal diameter of the syringe is tapered too much, then the shot size will decrease as the fluid travels down toward the bottom. To address this problem, Techcon offers various series of TPD valve systems.
Recommended Time/Pressure Dispensing Products: TS250 Dispenser | TS255 Dispenser | TS350 Precision Dispenser Controller | TS355 Precision Dispenser Controller
PINCH TUBE VALVE
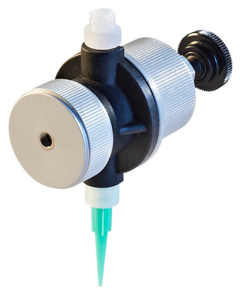
The simplest and most inexpensive TPD valve is the disposable pinch tube valve. It is designed to dispense small dots or continuous beads of low viscosity fluid. This air-actuated valve is operated by automatically opening and closing (pinching) a molded plastic tube assembly. The only part of the valve contacting the fluid is the disposable pinch tube assembly. This unique feature makes the valve perfectly suited for applications that use quick curing adhesives or highly aggressive fluids that might damage other types of valve bodies. Pinch tube valves are commonly used to dispense cyanoacrylate (CA) for general bonding applications or dispense two-component epoxies for potting applications. Benefits include its disposable path, lightweight, compact size, and simple operation.
Recommended Pinch Tube Valve: TS1212
DIAPHRAGM VALVE
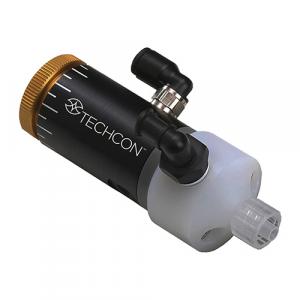
One drawback of the pinch valve is that some applications require frequent pinch tube replacement. In such cases, the diaphragm valve is a perfect alternative. Due to the resilience of the diaphragm material, it can last for millions of cycles before needing replacement. This pneumatic valve uses a diaphragm to open and close the fluid path. During the dispense cycle, the air pressure signal forces the diaphragm to pull back, creating an opening for the fluid to flow through. When the air signal stops, the internal spring pushes the diaphragm down to the closed position.
The unique component of this valve is the diaphragm. It is a solid barrier made from ultra-high-molecular-weight polyethylene (UHMWPE) to prevent moisture from the air cylinder from coming into contact with the fluid. This makes the valve an excellent choice to dispense moisture-sensitive fluid like cyanoacrylate.
Other attributes that make this valve widely popular in the industry are its compact size, lightweight, simple cleaning and maintenance, and adjustable stroke control that can produce a shot size as small as 0.002 cc.
Virtually any low to medium viscosity fluid can be dispensed using one of the diaphragm valve variations. Applications of this valve range from dispensing moisture-sensitive adhesives for general bonding applications, to dispensing UV-cured adhesives in the medical device industry, to spin coating applications in the semiconductor industry.
Recommended Diaphragm Valves: TS5622 | TS5625DMP
NEEDLE VALVE
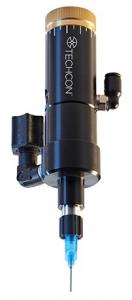
For applications that require micro-dot-sized deposits of less than 0.002 cc, the micro-shot needle valve is an ideal choice, which can easily deposit shot sizes as small as 0.0005 cc. Thanks to the unique design of the shut-off mechanism located inside the dispense tip, the “dead fluid” volume is virtually eliminated. The smallest needle size of 32 gauge can be used without dripping between dispense cycles.
The needle valve is a pneumatically triggered single-acting valve. An air pressure signal lifts the piston-driven needle away from its seat, allowing fluid under pressure to flow through. When the cycle is completed, the internal compression spring pushes the needle back into the closed position. Higher viscosity fluid, up to 100,000 cps, can be dispensed accurately with this valve, however moisture-sensitive fluid, and quick curing adhesives are not to be used.
Some recommended fluids are UV adhesives, solvents, inks, oils, primers, and activators. Typical applications include dispensing small amounts of UV adhesive to bond the speaker of a hearing aid device and dispensing small dots of ink for marking applications.
Recommended Needle Valves: TS5420 Precision Needle Valve | TS5440 Microshot Needle Valve
SPOOL VALVE
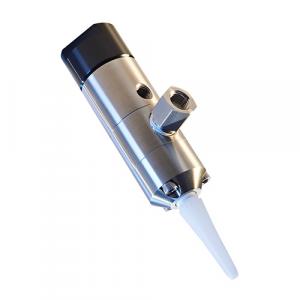
Valves described above have one thing in common: they are not designed to dispense high-viscosity fluid in high-volume applications. For applications requiring precision high-viscosity fluid dispensing, Techcon offers the spool valve series. High viscosity fluid, up to 3 million cps, is dispensable through these heavy-duty spool valves.
The valves use an air-actuated piston to open and close the fluid’s path. However, contrary to the needle valve, the air pressure signal drives the piston down to open the fluid path. When the dispense cycle is done, the internal compression spring lifts the piston up to keep the valve in the closed position. The pullback action of the piston in the closing cycle creates a natural “suck-back” action. This feature is very effective for preventing drips when dispensing high-viscosity fluid such as silicones, greases, and sealants.
The most common application of spool valves is dispensing sealant for form-in-place gaskets, dispensing grease for automotive applications, and filling material into syringes or cartridges for the material packaging industry.
Recommended Spool Valves: TS5322 Mini Spool Valve | TS941 Spool Valve
ROTARY AUGER VALVE
To address fluctuations in viscosity and avoid the need to adjust fluid pressure in the valve, Techcon developed the Rotary Displacement Dispensing technique.
The technique uses a rotary feed screw (auger) coupled with a precision DC motor to dispense fluid with a rotary displacement action. The unique design ensures fluid is constantly present at the feed screw inlet while the controlled rotation of the feed screw dispenses fluid from the feed point out to the dispense tip. A dot size of 0.010” (0.25 mm) in diameter can be achieved with a high percentage of repeatability.
Due to its versatility, high accuracy, and ease of setup, the TS7000 Series Rotary Valve can be a preferred choice for your application. It can dispense virtually any fluid of viscosity between 30,000 and 1,300,000 cps, including difficult materials like solder paste. In fact, it is the only valve that can dispense solder paste consistently.
A disposable material path version of the TS5000DMP Series is available for applications that use two-component adhesives, quick curing adhesives, or highly abrasive fluid. Wetted parts are fully disposable, eliminating the need for cleaning and repair.
The rotary valve is an excellent choice for electronics manufacturers dispensing surface mount adhesives, silver-filled epoxies, encapsulant materials, or solder.
Recommended Rotary Auger Valves: TS5000DMP | TS7000-DCX
SPRAY VALVE
Spray Valves are designed for precise spray applications of low viscosity materials and adhesives, typically less than 1,000 cps, with no overspray. Total control of the spray cycle is provided by adjustable fluid flow and precise control of pre-spray, atomizing air, and post-spray with the smart controller, while an external stroke control makes it easy for the operator to fine-tune fluid flow. Maintenance is made simple by the elimination of troublesome spring-loaded needle packings. Downtime is virtually eliminated with only one seal to replace during normal maintenance.
The Techcon TS5540 Series Spray Valves come with FDA-Compliant 303 stainless steel construction in both air cylinder and fluid housing. A field-replaceable Delrin® seat provides positive shut-off and very long life cycles. The compact design allows for easy integration into automated applications.
Two nozzle types are available: cone (R) for round spray patterns and fan (F) for elliptical spray.
Typical applications best suited for spray valves include spraying conformal coating onto PCBAs, applying lubricating oil, and spraying ink to indicate Pass or Fail.
Recommended Spray Valve: TS5540 Spray Valve | TS5520 Fine Mist Spray
PROGRESSIVE CAVITY (PC) PUMP
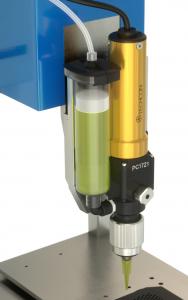
If your application calls for the highest levels of accuracy and repeatability, the progressive cavity (PC) pump is the most volumetrically precise dispensing system you can find, with variation as low as +/-1%.
A PC pump like the Techcon TS8100 Series Progressive Cavity (PC) Pump achieves this level of accuracy using a unique rotor and stator design. A single-helix-shaped rotor rotates inside a double-helix cavity stator, creating uniform air-tight cavities. These cavities move the fluid spirally along the axis of the pump as the rotor turns, delivering exact volumes of material with each revolution.
Because of progressive cavity technology, PC pumps are not affected by changes in material temperature, pressure, or viscosity, and can reliably dispense materials up to 3000,000 cps.
The easy-to-clean TS8100 achieves accurate dispense amounts as small as 0.001 ml, with no dripping of any viscosity fluid. The volumetric fluid flow does not change the size or shape of the material, making it compatible with many fluid types, including abrasive materials.
For more information about PC pumps, check out our blog, “Why Progressive Cavity (PC) Pump is the Best Dispensing Pump for Underfill Accuracy”
PC Pumps are often used for dispensing underfill, encapsulation and potting applications, applying lubrication on automotive parts, and dispensing pastes and flux.
Recommended PC Pump: TS8100
JET VALVE
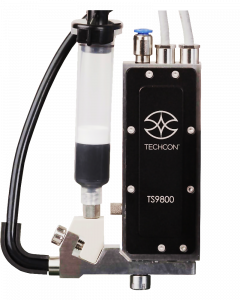
If dispensing speed is your main requirement, look to a jet valve system for the fastest dispensing available. A PC pump or auger valve will top out at around five deposits per second, which is perfectly adequate for some applications. For applications requiring greater speed, even a relatively slow jet valve can deposit as many as 500 shots per second.
Much of this speed advantage comes from the simple fact that a jet valve does not need to contact the substrate to make a deposit, like with other dispensing techniques. A jet valve simply glides over the substrate, “jetting” the fluid, even into otherwise difficult-to-reach spots on uneven surfaces.
Techcon took jetting technology a step further with the introduction of the TS9800 Jet Valve System, based on piezoelectric technology. With speeds of 1500 Hz continuous, 2000 Hz burst, TS9800 is the fastest dispensing system on the market. With this outstanding speed, the TS9800 is still able to deliver dispense accuracy of +/- 3%, with deposits as small as 0.5 nanoliters.
To learn how a piezo-actuated jet valve works, read our blog, “State-of-the-Art Dispensing: Piezo Jet Valves.”
Key applications for jet valve systems include applying die attach adhesives, underfill, dispensing conductive adhesives, LED encapsulation, and form-in-place gasket applications.
Recommended Jet Valve: TS9800
CONCLUSION
Selecting the right dispensing equipment is the most important part of the manufacturing process, so a detailed analysis of your application is required from the equipment supplier.
Techcon is one of the few dispensing companies that offer a wide product range to suit every level of dispensing application requirement.
Techcon is happy to test your materials to determine which dispensing system will best fit your application. Contact us today for more information.
– – –
ABOUT TECHCON: Since 1961, Techcon has provided precision fluid and adhesive dispensing equipment to a range of service industries, including industrial assembly, aerospace, military, material packaging, medical device, and electronics. Techcon products are renowned for their superior accuracy and durability, yielding improved industrial hygiene and enhanced productivity. Backed by our expert engineering team, Techcon, an OK International company, is delivering smarter, cleaner, more durable solutions. For more information, keep browsing Techcon.com.