5 min. read
The use of two-part (2K) adhesives, also known as reactive or structural adhesives, has advantages over one-part (1K) adhesives in production environments. But working with 2K materials can pose many challenges for manufacturers, especially for those who require precise mix ratios and output volumes.
Let’s look at the differences between 1K and 2K adhesives, the challenges of 2K materials, and the advantages of metering and mixing two-part adhesives using progressive cavity dispensing technologies.
Topics Covered:
2-Part Adhesives are Stronger Than 1-Part Adhesives
2K Materials Must be Measured and Mixed Precisely
Progressive Cavity Pumps are Incredibly Precise
Viscosity Changes Are Not an Issue with PC Pumps
Meter Mix With 2 PC Pumps for The Ultimate Reliability and Precision
Summary
2-Part Adhesives are Stronger Than 1-Part Adhesives
It is true, in some environments 1-component adhesives can be easier to use, as they can be applied right from the container without mixing, metering, or degassing. And 1-component adhesives may only require heat or light to initiate the curing process.
But, 2-component adhesives are stronger than their one-part cousins, because of their molecular bond structure. While there are many types of 2K adhesives, epoxy systems tend to be the most commonly used in electronics. These 2K adhesives require users to mix a resin and hardener, where the hardeners trigger the polymerization required for curing. With the mixing of the resin and hardeners, either by hand or by some mechanical method, an exothermic reaction occurs as the molecules cross-link.
Many adhesives manufacturers also offer pre-mixed and frozen formulations, enabling materials to be dispensed without mixing or metering. These alternatives require arduous storage and handling to maintain material integrity, significantly complicating storage and handling requirements.
2K Materials Must be Measured and Mixed Precisely
A major challenge of 2K adhesives is having to mix the resins and hardeners.
Incorrect resin mix ratios will affect the strength of cured adhesive. Specifically, joints bonded with adhesive compositions with excessive hardener may lead to compromised bond strength properties. Incorrect mix ratios lead to failures, especially at elevated temperatures (like within an electronics assembly).
Precise mixing ratios are critical to the final bond strength of 2K adhesives. Choosing the right meter mixing process and equipment is critical to managing consistency in the performance of the final product.
The good news is there are a lot of great options, allowing for consistent mixing of materials to ensure correct ratios. And these systems can easily be attached to standardized assembly equipment. Recent innovations in micrometer mixers or pumps include combining two highly reliable progressive cavity pumps together to automate the mix ratio processes.
Progressive Cavity Pumps are Incredibly Precise
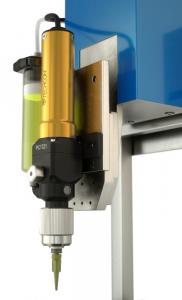
In 1930, The University of Paris awarded Rene Moineau a Doctor of Science for his work on designing a compressor for jet engines and applying this principle to pumping systems. His pioneering work and dissertation laid the foundation for the progressive cavity pump (PC pump), now commonly used in multiple industrial applications.
PC pumps are fundamentally fixed flow rate pumps. The basic workings include a single-helix-shaped rotor that rotates inside a stator with a double-helix cavity. The rotor is typically made of stainless steel or other hardened metals. The stator is usually made of an elastomer that can be molded into exact dimensions, ensuring a precise fit.
With the rotor inserted into the stator, watertight cavities are created, which move fluid spirally along the axis of the pump as the rotor turns within the stator. The PC pump then delivers an exacting volume of material for each revolution of the rotor.
PC pumps are extremely versatile and can be used in many different pumping applications. They work well with abrasive materials commonly used in 2K structural adhesives and potting applications.
Viscosity Changes Are Not an Issue with PC Pumps.
The shelf life or pot life of an adhesive is typically measured as the increase in a material’s viscosity. As the material ages, the viscosity tends to increase and be highly susceptible to changes in temperature (fluid viscosity often increases with decreasing temperature, and vice versa). These viscosity changes can have large repercussions on dispensing accuracy for non-volumetric pumps and valves.
One of the clear advantages of using PC pumps is that they are relatively unaffected by changes in material viscosity since they are volumetric pumps (meaning the volume dispensed is consistently accurate). With a progressive cavity pump, the mechanical and volumetric efficiency goes up as the viscosity increases, due to frictional characteristics between the material and the moving rotor.
Since the rotor and stator create volumetric pockets, the net effect is higher pressure within the pump, which increases the pump’s efficiency. A progressive cavity pump is therefore ideal for applications where adhesives are known to change from batch to batch, or over their shelf life.
Meter Mix With 2 PC Pumps for The Ultimate Reliability and Precision
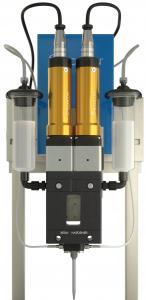
Integrating two PC pumps into a meter mixing system like Techcon’s new TS8200D Micro-Meter Mix provides the benefits and accuracy of progressive cavity pumps, with the added benefit of allowing for various mix ratios with software control.
Each PC pump can be set up to turn at different speeds, allowing for precise mixing, no matter the mix ratio. Smart controllers like the Techcon TS580D-MM set different rotational speeds on each pump to accommodate various mix ratio requirements. And with volumetric accuracies of +/- 1% on each PC pump, manufacturers can rest assured their final product will have the right mix of hardener and resin.
When integrated with a multi-axis gantry robot, PC pumps can provide precise and efficient dispensing solutions for high-volume production, delivering highly accurate volumetric dispensing and reliable flow rates. For many applications, incorporating progressive cavity pumps helps minimize product waste while providing operational efficiencies.
Summary
Manufacturers of electronic systems are turning to 2K adhesives for improved quality, productivity, and efficiency. There are multiple chemistries that use 2K materials from epoxies, silicones, urethanes, and acrylics, each with different performance properties that are often not available in single-part products.
2K adhesives offer a number of benefits over single-component adhesives, including cure times and cure characteristics, controlled by reactive chemistry. Single-component adhesives rely on heat, light, or other environmental initiators to kick off the curing process. Additionally, material handling and storage of 2K materials are typically much easier to manage, compared to single-component formulations.
Custom formulations can also be found in 2K properties, such as controlled shrinkage, room-temperature cure, heat transfer ability, electrical insulation, and chemical compatibility. This makes it much easier to design formulations for specific applications.
2K adhesives are often used in electronics where there is the need to bond, protect, and secure essential assemblies. With the ever-increasing demand for accuracy and repeatability, meter mixing has become an essential part of the production process, including high-volume and high-reliability applications such as automotive, aerospace, and defensive systems. These 2K materials ensure the long-term reliability of finished assemblies in harsh environments.
Two-part mixing systems integrated with software controllers and PC pumps, like the new TS8200D Series Micro-Meter Mix Dispensing System, can deliver accurate mix ratios, with volumetric accuracies of +/- 1%. This enables blending hardeners and resins within precise formulations, regardless of material viscosity. Micrometer mix systems ensure changes in viscosity and shorter work life are not detrimental to the overall production process, ensuring consistency in the finished assemblies.
________________________
Techcon is proud to introduce the new TS8200D Series Micro-Meter Mix Dispensing System, for true volumetric dispensing of 2-component materials. Meter, mix, and dispense 2K adhesives with +/- 1% volumetric variation, with no fear of cross-contamination and easy maintenance and cleanup. Learn more about the new TS8200D at Techcon.com