The compact camera module (CCM) market is experiencing exceptional growth, as consumer demand for high-quality cameras is on the rise. Smartphones are driving much of that growth, as photo and video sharing apps continue to increase in popularity. The demand for webcams reached an all-time high in 2020 and 2021 as COVID-19 forced millions of workers to start telecommuting. And today, cameras modules are an expected feature in everything from automobiles to doorbells.
This growth in demand creates the need for manufacturers to maximize output, and the challenge of manufacturing cutting-edge products like CCMs remains the same: how do operations maximize manufacturing speeds while ensuring product quality?
Challenges of Epoxy Dispensing in the Die Attach Process
During the manufacturing of camera modules, precise applications of adhesive are used to bond many of the individual parts together: lens onto the lens mount, the mount onto the camera sensor, etc. One of the more exacting processes is die attach, or die bonding, for the attachment of the image sensor.
Die Attach Speed is Dictated by the Dispensing Technology
Die attach is a multi-step process, including epoxy application, die picking and placing, curing, etc. The dispensing of the epoxy takes about 65% of the total die attach process time. More than any other part of the process, the adhesive dispensing is an area of possible speed improvement. If the operation speeds up the application of die attach epoxy, throughput increases dramatically.
Die Attach Epoxy Volumes Must Be Exact
Die sizes are increasing to accommodate ever higher camera resolutions. And these larger dies require even greater precision in the volume and placement of the die bonding adhesive. Inconsistencies in dispensing can lead to die lifting, die cracking, contamination of the die by the epoxy, and other die failures. It is imperative to maintain output that the epoxy placement and volume be exact at every application.
Advantages of Jet Valves Over Contact-Based Needle Valves
It is through the precise and repeatable dispensing of the die bonding adhesive that quality output is maintained. Currently, there are several valve types successfully used in the dispensing of epoxy for die bonding: time/pressure, auger pump, positive displacement pump, and jetting valve.
Contact-Based Dispensing Systems
Time/pressure, auger pump, and positive displacement pump valves all fall under the category of “contact-based” valves. The valve’s dispensing needle or nozzle is brought into contact with the substrate to place the fluid. Although the internal mechanics of each differ in how they measure and dispense material, all three systems boast accuracy and versatility well within the demands of camera die attach.
Non-Contact Based Jet Valve Systems
Jet valves, on the other hand, are non-contact dispensing valves. The valve literally shoots the fluid to be dispensed onto the substrate from above. Jet valves are very accurate, even when dispensing material into hard-to-reach areas on uneven substrates.
Where jet valves really shine over contact-based systems is in their speed. A standard pneumatic jet valve easily achieves dispensing speeds 10x that of the other systems.
A jet valve’s inherent advantage over contact-based needle valves is they don’t waste time moving on the “z-axis.” After each dispensing episode, a needle valve must be lifted, moved into its next position over the substrate, lowered, and dispense again. All of this up and down motion is very time-consuming and not required of a jet valve.
In contrast, a jet valve glides at a fixed height above the substrate. This saves a lot of production time. And, since there is no needle potentially crashing into the substrate upon contact, there is less damage and waste.
How Piezo Jet Valve Systems Meet The Challenges Of Precision Adhesive Dispensing
Techcon, the industry leader in fluid dispensing technologies, examined the challenges of precise material application and set out to rethink jet valve technology. Their answer to remarkably fast and accurate jetting is the Techcon TS9800 Series Piezo Actuated Jet Valve.
Piezo Jet Valves Outperform Pneumatic Jet Valves
Unlike a more common pneumatic jet valve, a piezo jet valve does not rely on air pressure to dispense. The fluid starts inside the valve, between the piston and the nozzle. A piezo crystal oscillates up and down at a high rate of speed, generating kinetic energy that forces the fluid to shoot out under carefully controlled pressure.
A perfect bead of material is shot out precisely at the target location, over and over, up to 2,000 times a second. This is a dispense rate of up to 2x that of a pneumatic jet valve.
The TS9800 Piezo Jet Valve achieves incredibly small dispensing volumes, with micro shot sizes as small as 0.5 nanoliters. With its ability to accurately dispense fluids of viscosities up to 2 million centipoises, operations are free to use whatever die bonding materials are best for the job.
This resolution does not come at the price of speed. The TS9800 jets at up to 1,500 micro shots per second continuous, up to 2,000 burst, with 97% accuracy.
This combination of small shot sizes, accuracy, and speed makes a piezo jet valve the ideal solution for achieving consistent bond lines for die attach, especially where maximizing output is desired.
Dial In the Ideal Settings at the Controller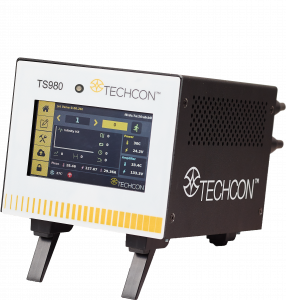
These tiny dots are achieved by not only making use of tiny aperture nozzles but by the flexibility to fine-tune both material and jetting pressure through the controller. The Techcon TS980 Controller offers an intuitive touchscreen interface to quickly and easily dial in parameters. Equipped with a standard internet connection through ethernet, the TS980 can be monitored, adjusted, and recorded from anywhere.
Getting the right balance of material pressure, jetting pressure, etc. for your application can be challenging. Techcon offers to test your material in their labs to make sure the TS9800 is the dispensing solution for your operation and determine the best parameter settings for your needs.
Piezo Jet Valve Buying Considerations
If you are considering switching to the power of a piezo jet valve system, there are a few things to consider:
Not Every Jet Valve is a Piezo Jet Valve
If a product is called a “jet valve,” that doesn’t mean it is necessarily a piezo jet valve. Piezo jet valve technology is relatively new, so most valves referred to as “jet valves” are pneumatic valves. Make sure you’re getting the added speed benefit of piezo technology, up to 2x faster than a pneumatic jet valve.
Size Matters
The relative size, weight, and footprint of the valve may be a consideration. For benchtop work, a smaller valve like the TS9800 means smaller work area demands and more efficient use of factory space. For automation, the TS9800 is easily combined with robotics and other devices to achieve fully automated best-in-class results.
Quality Check
To achieve these amazing speeds and shot accuracy, a piezo jet valve needs to be manufactured to exact specifications. The tolerances on such precise components, like the nozzle and the tappet piston, are extremely tight, and producing them is beyond the abilities of many parts fabricators. Inferior valves will lead to dispensing inaccuracies, inconsistent speeds, frequent failures, and other issues that greatly impact productivity and output quality.
The Support from the Manufacturer Matters
Be sure you are buying from a company that offers a wide range of technical support, configuration assistance, and other troubleshooting services. As mentioned, Techcon works with all our customers to ensure their system gets up and running as expected and stays that way.
Take Away
The die attach process in camera module manufacturing is an exacting one. To maximize output, you need a dispensing valve that can meet the challenges of precise placement of die attach materials at exact volumes at high speed. With the cutting-edge Techcon TS9800 Piezo Actuated Jet Valve, achieve speeds of up to 1,500 shots continuous, with shot sizes as small as 0.5 nL, using material viscosities up to 2 million centipoises. Its compact design makes it versatile; its outstanding build quality makes it a workhorse. The ultimate in high speed, high accuracy dispensing is a piezo jet valve from Techcon.
For more information, go to info.Techcon.com/jet-valves.
TS9800 Series Jet Valve Resources
More Information | User Guide | Technical Data Sheet | Spare Parts Guide
ABOUT TECHCON: Since 1961, Techcon has provided precision fluid and adhesive dispensing equipment to a range of service industries, including industrial assembly, aerospace, military, material packaging, medical device, and electronics. Techcon products are renowned for their superior accuracy and durability, yielding improved industrial hygiene and enhanced productivity. Backed by our expert engineering team, Techcon, an OK International company, is delivering smarter, cleaner, more durable solutions. For more information, keep browsing techcon.com.