As PCBAs have become more tightly packed with through-hole components, bottom-side SMT devices, and ever more crowded circuitry, the precision of surface mount adhesive (SMA) dispensing is more critical than ever. But in the ever-competitive world of electronics manufacturing, precision is never enough. We need precision dispensing and ever greater speeds.
Precision + Speed = Increased Throughput – Rework/Waste.
We’re going to look at several options of applying surface mount adhesive, to see how best to increase output.
Understanding the Three SMA Application Methods
1. Pin Transfer
When using the pin transfer method, an application-specific array of pins is used, that matches the required pattern of adhesive dots to be applied to the printed circuit board or substrate. The pins are dipped into adhesive, moved into position, and then lowered to touch the work area’s surface. Upon contact, the adhesive is “transferred” from the pins to the board.
This is one of the fastest methods of applying adhesive to a PCB, as the adhesive is applied to the entire board in a single application. This makes it a viable method for high-volume operations with long production runs.
Pros & Cons of Pin Transfer
PROS:
- Very fast – since the adhesive is applied to the entire surface of the PCB in one pass
- Good for high-volume operations where there are few changes to boards over time
CONS:
- Requires creating a dedicated pin array for each board design
- More time spent in the set-up and changeover process
- These single-purpose tools must be cleaned, stored, and managed between uses
- Requires very specific adhesive properties for the process to work
- Often can only be used on unpopulated PCBs
2. Screen Printing
In screen printing, a screen or stencil is created to perfectly match the pattern required for the adhesive on the PCB or substrate. The stencil is carefully aligned with the board, and the adhesive is applied to the screen and drawn along its length with a squeegee. Holes in the screen or stencil allow the adhesive to pass through onto the board.
Pros & Cons of Screen Printing
PROS:
- Very fast – since the adhesive is applied to the entire surface of the PCB in one pass
- Good for high-volume operations with little change to boards
CONS:
- Requires creating a dedicated screen for each board design
- More time spent in the set-up and changeover process
- These single-purpose tools must be cleaned, stored, and managed between uses
- Often these methods can only be used on unpopulated PCBs
3. Dispensing
Often, surface mount adhesive is applied using traditional fluid dispensing techniques, like Time/Pressure dispensing, Auger Valves, Progressive Cavity Pumps, and Jet Valves.
The key difference among these methods, when it comes to their overall speed, is whether they are contact-based or non-contact-based systems.
Contact-Based Dispensing Systems
Time/Pressure systems, Auger valves, and PC Pumps all work on fundamentally different principles, but their speed is dictated by one key factor: their dispensing method requires the dispensing tip contacts the board. The dispense head is moved into position, lowered to the correct distance from the PCB, and the adhesive is pushed out. The dispense head is raised, the fluid is sheared off, and the head is moved to its next position.
All of that up and down movement on the Z-axis is time-consuming.
Pros & Cons of Contact-Based Systems
PROS:
- More adaptable to differing board designs, without having to create a unique pin array or screen for each application
- PC Pumps (in particular) offer high dispense accuracy (+/- 1%)
- The most common and familiar method of applying SMA
CONS :
- Z-axis movement of dispense head is inherently time-consuming
- Dwell time & dispense height accuracy is required for repeatability
- Time/Pressure and auger valve accuracy suffer from fluctuations in viscosity
- Possibility of stringing
Non-Contact Jet Valve Dispensing
Jet valves, on the other hand, offer a major advance over other methods, due to their sheer dispensing speed. Even a mid-level jet valve will dispense 20 times faster than a PC pump or auger valve.
And jet valves do not need to contact the work area. They are positioned to fly over the PCB at a fixed height, jetting the SMA from above. Between the ability to dispense quickly, and not needing to move up and down on the Z-axis, jet valves are incredibly fast systems.
Pros & Cons of Non-Contact Jet Valve Systems
PROS :
- Fast dispensing rates
- Jetting from a fixed height means no time wasted on the Z-axis
- Can jet SMA into hard-to-reach places on uneven/populated boards
- Easily adaptable to multiple board designs and dispensing uses
- No likelihood of damaging the product due to needle crash
CONS :
- Not compatible with fluids with course fillers, like some solder pastes
For more information on the advantages and limitations, history, and development of contact and non-contact dispensing technology, see our white paper, “Jet Dispensing Technology – Shooting for Perfection.”
Pneumatic Jet Valve vs Piezo Jet Valve Dispensing
If the speed and flexibility of a jet valve system seem right for your surface mount adhesive dispensing needs, keep in mind there are two very distinct jet valve technologies on the market: pneumatic jet valves and piezo jet valves.
More common pneumatic jet valves use air pressure and mechanics to dispense. Piezoelectric jet valves, however, use an actuator to create very precise and high-speed motion within the valve, dispensing material at much greater speeds.
The process of the pneumatic jet valve opening, closing, and resetting only takes an extra 20 milliseconds compared to a piezo valve, but that extra time ads up quickly. The difference makes the piezo jet valve up to twice as fast as a pneumatic jet valve. For operations looking to maximize throughput, this is an outstanding increase in speed.
TS9800 Series Jet Valve Systems: The Fastest Dispensing System on The Market
Techcon’s answer to fast and precise dispensing is the new TS9800 Series Jet Valve System. This piezo-activated jet valve system achieves such outstanding results, it is the fastest non-contact dispensing system on the market.
TS9800 Jet Valve Features
- Dispensing frequencies up to 1500 Hz continuous, 2000 Hz burst
- Up to 97% dispensing accuracy
- Shot sizes as small as 0.5 nL
- Compatible with viscosities up to 2 million cps
- Optional fluid housing heater for better viscosity stabilization
All this amazing speed and accuracy would not be possible without the advanced features of the TS9800 Smart Controller.
TS980 Smart Controller Features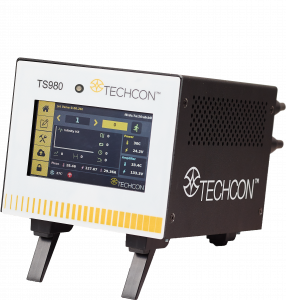
- Intuitive touch screen interface
- Quick and easy valve calibration
- Remote monitoring and parameter adjustment over internet connections
- Industry 4.0 compatible
Jet Valve Purchasing Considerations
There are several factors to consider when in the market for a jet valve system.
Valve Size and Integration
Consider the size, weight, and footprint of the valve itself, and how it will fit into the available factory space. Machine integrators maximize the speed of a jet valve by building them into high-end automation equipment and robotics systems.
Build Quality
All piezo jet valves are not created equal. Be aware that piezo jet valves are highly precise pieces of equipment and should be built to exacting standards. The tolerances of proper valve production are incredibly tight and producing them within those parameters may be impossible for some parts fabricators.
Lower-priced piezo jet valves can quickly develop problems, causing inaccurate dispensing, inconsistent speeds, and other failures that negatively impact productivity and quality. Be sure you are purchasing from a top dispensing valve manufacturer, like Techcon.
Consider The Level of Support from The Manufacturer
Determining whether a dispensing system is right for an operation is no small feat and should be undertaken with the help of a trusted manufacturer.
Getting the right balance of material pressure, jetting pressure, etc. for your application can be challenging. Techcon offers to test your SMA in their labs to make sure the TS9800 system is the dispensing solution for your operation and determine the best parameter settings for your needs.
Consider the availability of local repairs or service, lead times, and/or in-person or remote assistance after the sale.
Also consider the availability of compatible accessories and equipment to be teamed with the jet valves and other dispensing equipment in the operation, like robots and automation equipment, pressure tanks and feeding systems, dispense tips, and cartridges/syringes.
Price Considerations
Such cutting-edge technology comes at a price, and a piezo valve system is a larger investment than that of a contact-based dispensing system. Still, the lifecycle cost is surprisingly similar to older pneumatic systems, with the piezo assembly rated at around 1 billion cycles. If your manufacturing process would benefit from dispensing at the highest speed and with super-high precision, the investment is worth it.
For more information, visit TS9800 Series Jet Valve System, watch jet valve application videos, read technical documents, or book a demo.
ABOUT TECHCON: Since 1961, Techcon has provided precision fluid and adhesive dispensing equipment to a range of service industries, including industrial assembly, aerospace, military, material packaging, medical device, and electronics. Techcon products are renowned for their superior accuracy and durability, yielding improved industrial hygiene and enhanced productivity. Backed by our expert engineering team, Techcon, an OK International company, is delivering smarter, cleaner, more durable solutions. For more information, keep browsing Techcon.com.